
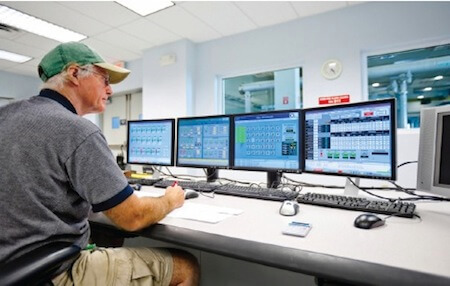
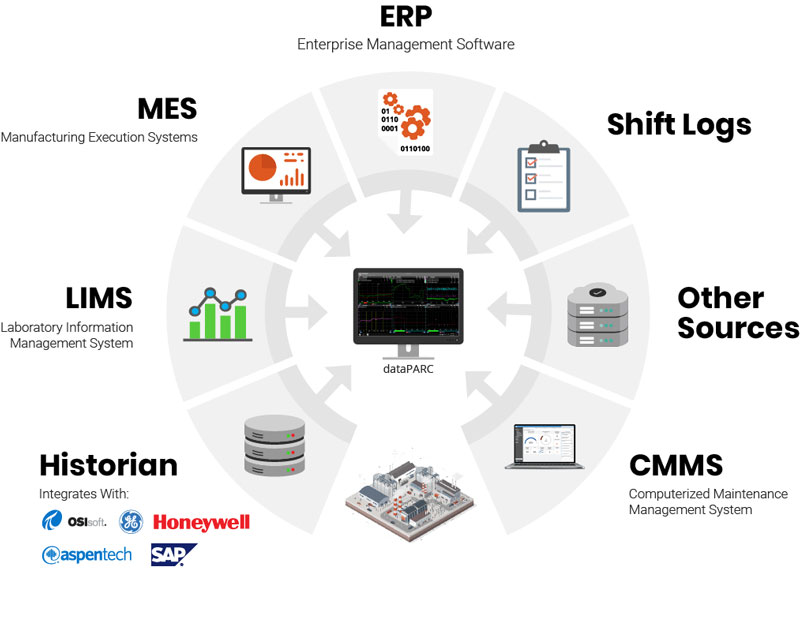
- Computerized maintenance management system cmms software update#
- Computerized maintenance management system cmms software software#
Computerized maintenance management system cmms software software#
On-premise: In this system, maintenance data is managed by an in-house software system. Generally, a computer maintenance management system is divided into two types.

Then the management of the organization takes the reports and analyzes them. It helps to complete the entry with valuable data and generates accurate reports. Even an administrator can create a mandatory field that the technician should fill before closing the work orders. If the equipment crosses the predefined threshold line, an email is sent automatically to the technician or maintenance team members.Ĭomputerized maintenance management systems allow the organization to set the system as per its requirements. In addition, it can be programmed to find out the difference in asset conditions.
Computerized maintenance management system cmms software update#
Now, computerized maintenance management systems process these data and update the records of the asset. The webmaster or technician updates the work order with new data like meter reading, time spent, etc., and the work order completes. When a work order generates, it is assigned to a webmaster or a maintenance team and equipment. How do computer maintenance management systems work? It is helpful to the industries like hospitals, oil & gas production, manufacturing industries, power generation, construction industries, transportation, government, etc. Mobile maintenance: With the help of mobile devices like smartphones, the technician or maintenance team members can access system data.Work order management: Automates work order generation, reserves the information like the work order number, work order type (repair or replace), tracks the downtime, and also records planned and actual costs.Preventive maintenance: Helps to reduce the equipment downtime.Inventory control: Helps to track inventory costs and helps to manage suppliers.Asset management: Stores and shares information about assets like equipment model, type, costs, repair information, safety measures, warranties, etc.Employee management: Helps to allocate the tasks to the employees and schedules their shifts.Equipment recording and tracking: Tracks the availability of equipment, records the equipment certification.
